The Ultimate Guide to Liquid Mixing Tanks: Structure, Features, and Applications
Explore the essential components and functionalities of liquid mixing tanks, including structure, mixing, homogenizing, heating, circulation, weighing systems, and more.
- What Are Liquid Mixing Tanks?
- Understanding the Structure of Liquid Mixing Tanks
- Layer Structure of Liquid Mixing Tanks
- The Role of the Agitator in Mixing
- Key Functions of Liquid Mixing Tanks
- Mixing and Dispersing Liquids
- Homogenizing Liquids for Uniformity
- Advanced Features in Liquid Mixing Tanks
- Heating Systems for Temperature Control
- Circulation for Consistent Mixing
- Weighing Systems for Precise Ingredient Measurement
- Choosing the Right Liquid Mixing Tank for Your Needs
- Tank Material
- Mixing Capacity and Volume
- Agitator Design and Speed
- Applications of Liquid Mixing Tanks Across Industries
- Food and Beverage Industry
- Pharmaceutical Industry
- Cosmetics and Personal Care Products
- Chemical Manufacturing
- Conclusion: The Essential Role of Liquid Mixing Tanks in Modern Manufacturing
- FAQs
What Are Liquid Mixing Tanks?
Liquid mixing tanks are vital components in industries such as food production, cosmetics, pharmaceuticals, and chemical manufacturing. They are designed to blend, disperse, and homogenize liquids efficiently to achieve a uniform mixture. The effectiveness of the mixing process significantly impacts the quality of the final product, whether it’s a liquid detergent, beverage, or pharmaceutical formulation.
In this comprehensive guide, we’ll explore the key features, benefits, and functionalities of liquid mixing tanks, including their layer structure, mixing methods, and additional components like heating systems and weighing scales.
Understanding the Structure of Liquid Mixing Tanks
The design of a liquid mixing tank is critical for its performance. A well-constructed tank ensures smooth operation, improved mixing quality, and long-term durability. Here's a look at the typical structure of these tanks:
Layer Structure of Liquid Mixing Tanks
The layer structure of a liquid mixing tank often includes multiple layers that serve specific purposes. These layers can be divided into:
Inner Layer: This is typically where the liquid mixture resides. It’s made from high-quality materials such as stainless steel to prevent corrosion and contamination.
Insulation Layer: Surrounding the inner layer, the insulation helps maintain the temperature of the contents and prevents heat loss.
Outer Shell: The outermost layer provides the tank with structural integrity and protection from external factors, like physical damage and harsh environmental conditions.
Each layer is designed to improve the mixing process, maintain temperature control, and ensure the safety of the tank during operation.
The Role of the Agitator in Mixing
A key element in the mixing tank is the agitator. Agitators come in different shapes and sizes, depending on the viscosity of the liquid and the desired end product. They can include:
Helical Blades: Used for liquids of higher viscosity.
Turbine Blades: Often used for fluids of lower viscosity, creating strong turbulence to aid in faster mixing.
The type of agitator selected will affect how well the ingredients blend, ensuring a consistent final product.
Key Functions of Liquid Mixing Tanks
Liquid mixing tanks have several essential functions that contribute to product quality and operational efficiency. Let’s explore these key functions in more detail.
Mixing and Dispersing Liquids
One of the primary functions of liquid mixing tanks is to mix and disperse different liquid ingredients to create a homogeneous blend. Whether it’s blending surfactants for detergents, dispersing additives in food products, or combining active ingredients in pharmaceuticals, the mixing process ensures uniform consistency.
Homogenizing Liquids for Uniformity
Homogenization is an advanced mixing process that breaks down particles and evenly distributes them throughout the liquid. This is essential in industries like cosmetics and pharmaceuticals, where consistency and uniformity are crucial to product efficacy. Liquid mixing tanks can be equipped with specialized homogenizing systems to achieve this level of uniformity, ensuring that all active ingredients are evenly distributed.
Advanced Features in Liquid Mixing Tanks
Modern liquid mixing tanks come with additional features that improve operational performance and efficiency.
Heating Systems for Temperature Control
Certain liquid products require precise temperature control to maintain the correct viscosity or chemical stability. Liquid mixing tanks with built-in heating systems can maintain the desired temperature of the contents during the mixing process. Heating elements are often integrated into the jacket or coil system of the tank, ensuring uniform heat distribution and preventing overheating.
Jacketed Tanks: These tanks are equipped with an external jacket that circulates hot water or steam around the tank to regulate the internal temperature.
Coil Heating: Coils placed inside the tank allow for more direct heat transfer, ensuring that the entire mixture reaches the desired temperature.
Circulation for Consistent Mixing
Some liquids, especially thicker ones, require continuous circulation for consistent mixing. Circulation pumps move the liquid inside the tank, ensuring that all ingredients are evenly distributed and that there are no stagnant areas within the mixture. This is particularly important when dealing with liquids that may separate or settle over time.
Weighing Systems for Precise Ingredient Measurement
For accurate formulation, many liquid mixing tanks come equipped with integrated weighing systems. These systems measure the weight of each ingredient being added to the tank, allowing operators to ensure precise proportions. This helps reduce errors in the final product and maintain consistency between batches.
Choosing the Right Liquid Mixing Tank for Your Needs
Selecting the right liquid mixing tank depends on several factors, including the nature of the liquid, production volume, and desired mixing outcome. Here’s what to consider:
Tank Material
The material of the mixing tank is crucial for preventing contamination and ensuring longevity. Stainless steel is the most common choice due to its corrosion resistance and ease of cleaning. However, depending on the specific needs of your product, you may need specialized materials like food-grade stainless steel or coated tanks for chemical applications.
Mixing Capacity and Volume
The tank size should be chosen based on your production requirements. Tanks come in various sizes, from small batch systems to large industrial-scale models. A larger tank can handle higher volumes, but it may require more powerful agitators and heating systems to ensure effective mixing.
Agitator Design and Speed
The agitator design should match the viscosity and flow properties of the liquids you’re working with. For example, high-viscosity liquids require slower agitation with specialized blades, while low-viscosity liquids may need faster, more intense mixing.
Applications of Liquid Mixing Tanks Across Industries
Liquid mixing tanks are indispensable in various industries. Let’s explore some of their key applications:
Food and Beverage Industry
In the food industry, liquid mixing tanks are used to prepare products like sauces, juices, soups, and dressings. The ability to maintain precise temperature control, along with mixing and homogenizing, ensures the quality and consistency of food products.
Pharmaceutical Industry
In pharmaceuticals, the formulation of liquid medicines and syrups relies heavily on liquid mixing tanks. Homogenization and precise ingredient measurement are critical to ensuring the efficacy and safety of medicinal products.
Cosmetics and Personal Care Products
Liquid mixing tanks are essential in the production of cosmetic products like lotions, shampoos, and liquid soaps. Mixing and dispersing active ingredients evenly ensures that the final product is consistent and high-quality.
Chemical Manufacturing
In chemical manufacturing, liquid mixing tanks are used to mix solvents, acids, and other chemicals. The ability to control temperature, circulation, and mixing speed is crucial to prevent chemical reactions that could affect the quality or safety of the products.
Conclusion: The Essential Role of Liquid Mixing Tanks in Modern Manufacturing
Liquid mixing tanks are a cornerstone of many industries, providing a vital service in creating consistent, high-quality products. From blending and homogenizing liquids to regulating temperature and ensuring accurate ingredient measurements, these tanks are essential in producing everything from detergents to pharmaceuticals. By choosing the right tank with the appropriate features, manufacturers can ensure the efficiency and quality of their production lines.
As industries continue to innovate and grow, the role of liquid mixing tanks will only increase in importance. Whether you're manufacturing food products, cosmetics, or chemicals, investing in a high-quality liquid mixing tank is key to achieving operational success and product excellence.
FAQs
1. What are the main components of a liquid mixing tank?
The main components include the tank body, agitator, heating system, circulation pump, and weighing system. These work together to mix, heat, and measure ingredients effectively.
2. Can liquid mixing tanks handle high-viscosity liquids?
Yes, liquid mixing tanks can be designed with specialized agitators and heating systems to handle high-viscosity liquids, ensuring efficient mixing and uniformity.
3. How do mixing tanks maintain temperature control?
Temperature control is maintained through jacketed tanks or coil heating systems that circulate hot water or steam around the tank to keep the contents at the desired temperature.
4. Are weighing systems necessary in liquid mixing tanks?
While not mandatory, weighing systems help ensure precise ingredient measurements, reducing errors and ensuring consistency across batches.
5. What industries use liquid mixing tanks?
Liquid mixing tanks are used in food and beverage, pharmaceutical, chemical, and cosmetics industries, among others, for mixing, homogenizing, and dispersing ingredients.
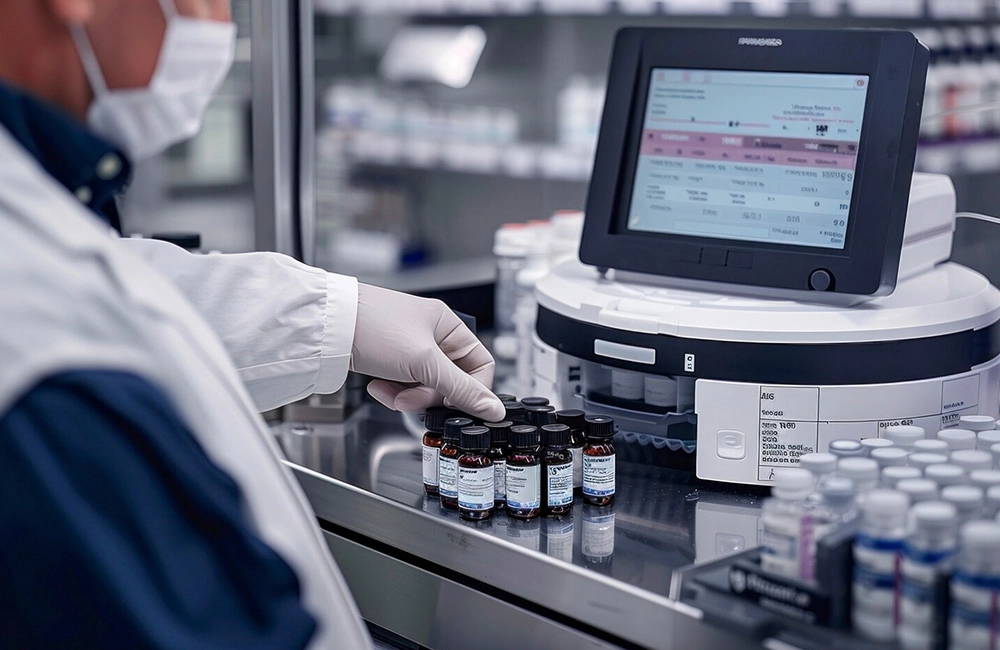
Regular Questions Asked by a Buyer and Answers About Liquid Production Line
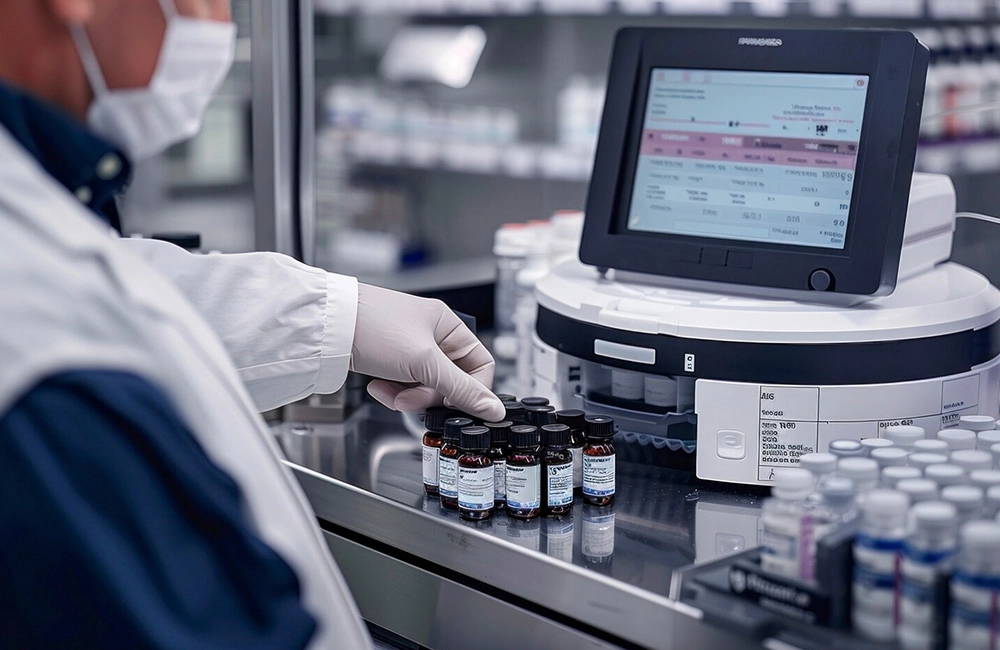
A Complete Guide to Liquid Soap Production Line, Liquid Soap Equipment Manufacturers, Solutions, and Homogenizer Mixing Tank
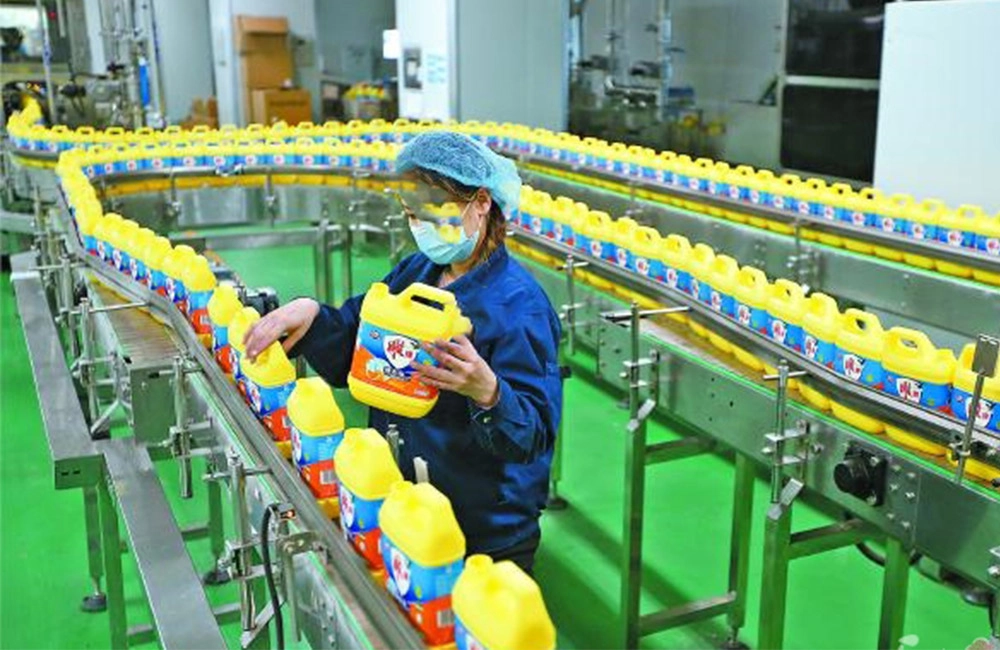
A Complete Guide to the Liquid Soap Production Line: Equipment, Process, and Key Considerations
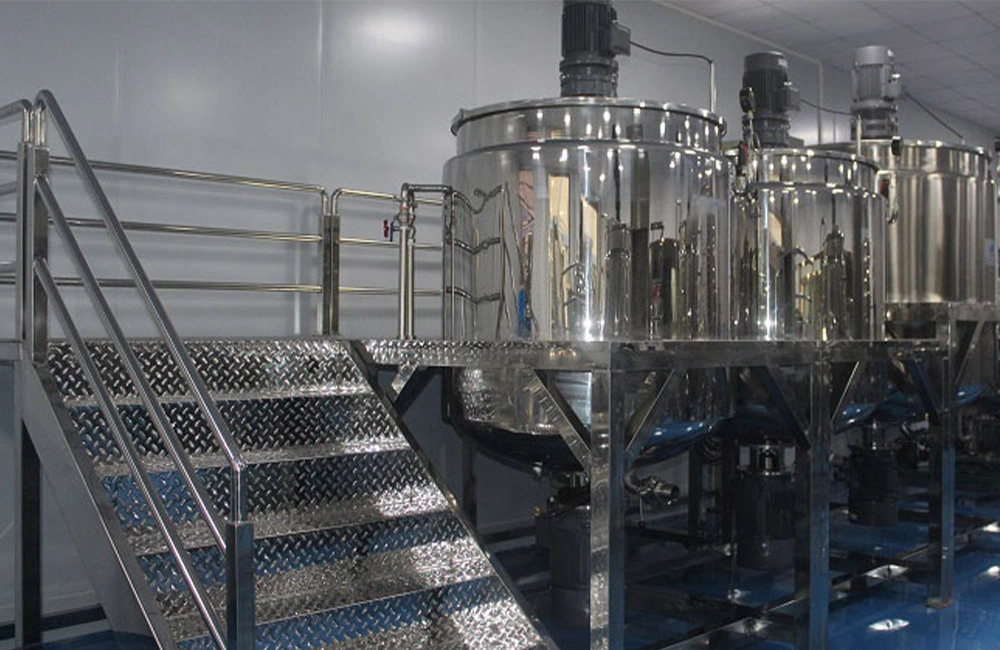
Everything You Need to Know About Homogenizer Mixer Machines: Benefits, Applications, and More
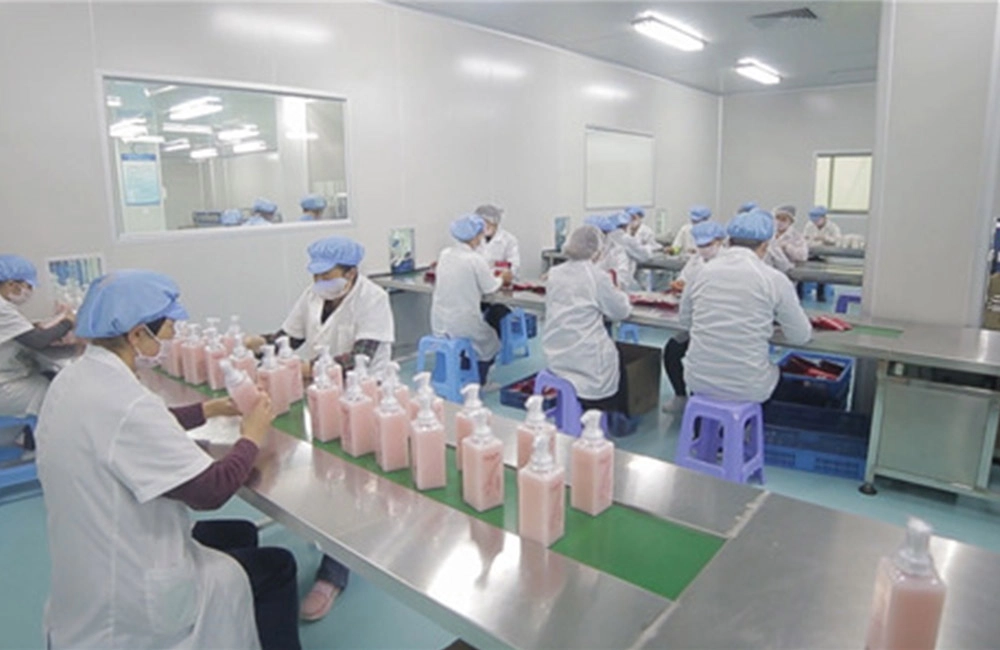
The Ultimate Guide to Cosmetic Production Line: Efficiency, Innovation, and Quality
FAQs
I don’t come to the company, how can I learn the machines?
We provide video & manual instructions of the machines you purchase and online service,as well as face-to-face teaching. Any questions or concerns,please feel free to contact our customer service for free information. If you come to the company,our technical staff will teach you hand by hand.
Detergent powder mixer
What’s the spraying system of the powder machine used for?
The spraying system is an optional function for adding liquid materials during mixing, such as perfume, essence...
Do you also provide formula of detergent powder if I purchase the detergent powder mixer machine?
Yes, Yuany offers technical support to help optimize formulas and adjust production processes, ensuring product stability and performance.
Powder Sachet Packaging Machine
Can the packaging machine for powder pack different weight in one machine?
Yes, the filling weight is adjustable with certain range. Client should tell the estimated filling weight to confirm. Different filling range may require different auger size.
Vacuum Emulsifier
What’s the brand of motor for this vacuum emulsifying mixer?
We have different brand of motor for clients to choose. The standard motor brand is Beide, optional choice is Siemens and ABB.
Leave a message
Have any questions or concerns about our products? Please leave us a message here, and our team will get back to you promptly.
Facebook
YouTube
LinkedIn
Whatsapp: +8613434139712