Regular Questions Asked by a Buyer and Answers About Liquid Production Line
Discover common questions buyers ask about liquid production lines, from costs to equipment types, and get clear, concise answers.
- Introduction
- What is a Liquid Production Line?
- Why Should I Invest in a Liquid Production Line?
- What Types of Liquid Production Lines Are Available?
- 1. Semi-Automatic Production Line
- 2. Fully Automatic Production Line
- 3. Custom Production Lines
- What Are the Key Components of a Liquid Production Line?
- 1. Mixing Equipment
- 2. Filling Machines
- 3. Packaging Machines
- 4. Inspection and Quality Control
- How Much Does a Liquid Production Line Cost?
- 1. Type of Line
- 2. Capacity
- 3. Features and Customization
- What is the Maintenance Process for a Liquid Production Line?
- 1. Regular Cleaning
- 2. Periodic Inspection
- 3. Software Updates
- How Long Does It Take to Set Up a Liquid Production Line?
- How Can I Ensure the Quality of My Liquid Products?
- 1. Automated Quality Control
- 2. Strict Raw Material Selection
- 3. Testing During Production
- What Are the Regulatory Requirements for Liquid Production Lines?
- Conclusion
- FAQs
Introduction
When considering the purchase of a liquid production line, potential buyers are bound to have numerous questions. The decision to invest in machinery for liquid production, such as for shower gels, detergents, or dishwashing liquids, involves a considerable financial commitment. To ensure that the investment is worthwhile and that the machinery meets specific needs, it's crucial to be well-informed. This article will answer some of the most frequent questions buyers ask about liquid production lines, giving you insights into everything from pricing to functionality and maintenance.
What is a Liquid Production Line?
A liquid production line is a complete system designed to manufacture liquid-based products such as soaps, shampoos, detergents, and more. These lines typically include several stages such as mixing, filling, packaging, and quality control. The machinery used in liquid production lines varies depending on the type of liquid being produced and the scale of production.
Why Should I Invest in a Liquid Production Line?
The decision to invest in a liquid production line is primarily driven by factors such as production efficiency, scalability, and product quality. Some key reasons to invest include:
Consistency and Precision: Automated systems reduce human error and ensure that the products are consistently of high quality.
Increased Production Capacity: A liquid production line can handle a higher volume of production than manual methods.
Cost Efficiency: Over time, automation saves labor costs and reduces waste.
By automating liquid production, businesses can scale operations faster while maintaining product quality.
What Types of Liquid Production Lines Are Available?
Liquid production lines come in various configurations depending on the product being produced and the level of automation required. Common types include:
1. Semi-Automatic Production Line
Semi-automatic systems involve a combination of manual labor and machine operations. These are ideal for small-scale operations or businesses just starting in liquid production.
2. Fully Automatic Production Line
Fully automatic lines are ideal for large-scale production. They are equipped with machines that handle everything from mixing to filling and packaging, all with minimal human intervention.
3. Custom Production Lines
Some manufacturers offer bespoke production lines tailored to specific product requirements. These may include specialized features such as temperature control for sensitive liquids or unique filling mechanisms for thicker formulations.
What Are the Key Components of a Liquid Production Line?
A liquid production line typically consists of several integral components. These include:
1. Mixing Equipment
The mixing equipment is used to combine raw ingredients into a consistent formula. Depending on the viscosity of the product, this could include mixers, blenders, or emulsifiers.
2. Filling Machines
Filling machines are responsible for accurately filling containers with the liquid product. These machines come in various designs to accommodate different bottle sizes, shapes, and materials.
3. Packaging Machines
After filling, the liquid product is typically sealed and labeled using packaging machines. These machines can also print batch numbers, expiry dates, and other important information on the packaging.
4. Inspection and Quality Control
To ensure that the products meet industry standards, quality control systems are incorporated into the production line. These can involve automated testing for consistency, viscosity, or appearance.
How Much Does a Liquid Production Line Cost?
The cost of a liquid production line can vary widely based on several factors:
1. Type of Line
A semi-automatic line is generally less expensive than a fully automatic one. The more automation and customization required, the higher the cost.
2. Capacity
Higher capacity lines capable of producing larger volumes per hour are typically more expensive. For instance, a line capable of filling 1,000 bottles per hour will generally cost more than one that fills 200 bottles per hour.
3. Features and Customization
Additional features such as automated filling, temperature control for delicate liquids, or specialized packaging solutions can increase the overall price.
As a rough estimate, a basic semi-automatic liquid production line could start at around $50,000, while fully automated systems might range from $100,000 to $500,000 or more.
What is the Maintenance Process for a Liquid Production Line?
Maintenance is a crucial aspect of ensuring the longevity and efficiency of your liquid production line. Some tips for maintaining your line include:
1. Regular Cleaning
Cleaning is essential, particularly in the food and cosmetic industries, where hygiene is a priority. Most liquid production lines are designed to be easily cleaned with minimal downtime.
2. Periodic Inspection
Scheduled inspections of all components such as pumps, motors, and filling nozzles ensure that everything is functioning correctly. Any worn-out parts should be replaced promptly to avoid production delays.
3. Software Updates
For automated systems that rely on software, keeping the software up to date ensures optimal performance and resolves potential glitches or bugs.
How Long Does It Take to Set Up a Liquid Production Line?
Setting up a liquid production line can take anywhere from a few weeks to several months, depending on the complexity and size of the line. Factors that influence setup time include:
Customization Needs: Custom systems or unique production requirements can extend the installation process.
Training: Proper training for your staff on how to operate the new machinery is essential for a smooth transition.
Testing: After installation, thorough testing and quality checks are necessary to ensure everything is functioning correctly.
How Can I Ensure the Quality of My Liquid Products?
Ensuring the quality of liquid products is paramount, especially in industries like cosmetics or pharmaceuticals, where product consistency and safety are critical. To achieve this, consider the following:
1. Automated Quality Control
Many modern liquid production lines incorporate automated quality control checks, such as viscosity measurement and inspection for defects.
2. Strict Raw Material Selection
Using high-quality raw materials and ingredients ensures that the final product is of the highest standard. Regular supplier audits and sourcing from reputable suppliers are vital.
3. Testing During Production
Frequent in-process testing helps detect inconsistencies or defects early on in the production cycle. This reduces the chance of defective products reaching the market.
What Are the Regulatory Requirements for Liquid Production Lines?
Depending on the region and industry, various regulations must be adhered to when setting up a liquid production line. For example:
Food and Beverage Industry: Must comply with health and safety regulations regarding ingredient sourcing, sanitation, and product labeling.
Cosmetic Industry: Must meet standards set by bodies like the FDA, ensuring the safety and efficacy of products.
Pharmaceutical Industry: Has even stricter regulations, including Good Manufacturing Practices (GMP) and other safety protocols.
Conclusion
Investing in a liquid production line can significantly enhance your production efficiency and product quality. However, it is crucial to understand the key components, types of lines available, and maintenance requirements before making a purchase. By asking the right questions and doing thorough research, you can make an informed decision that aligns with your business goals. Whether you're just starting out or scaling up, ensuring that your liquid production line is tailored to your needs will help you achieve long-term success.
FAQs
1. How often should I replace parts on my liquid production line?
Parts should be replaced based on usage, wear, and manufacturer guidelines. Generally, critical components like pumps and nozzles may need replacement every 1-2 years, depending on the production volume.
2. Can I upgrade my existing production line?
Yes, many manufacturers offer upgrades such as automation enhancements, increased capacity, or additional filling stations, allowing you to expand your existing system.
3. What is the energy consumption of a liquid production line?
Energy consumption varies based on the type of machinery, its capacity, and the complexity of the production process. On average, a fully automatic line consumes more energy than a semi-automatic one.
4. How can I improve the efficiency of my liquid production line?
Regular maintenance, upgrading to more efficient machinery, and optimizing production workflows are key to improving efficiency. Additionally, investing in automated quality checks can reduce production defects.
5. Is training necessary for operating a liquid production line?
Yes, proper training is crucial for ensuring operators can safely and efficiently manage the machinery. Many manufacturers offer training as part of the installation process.
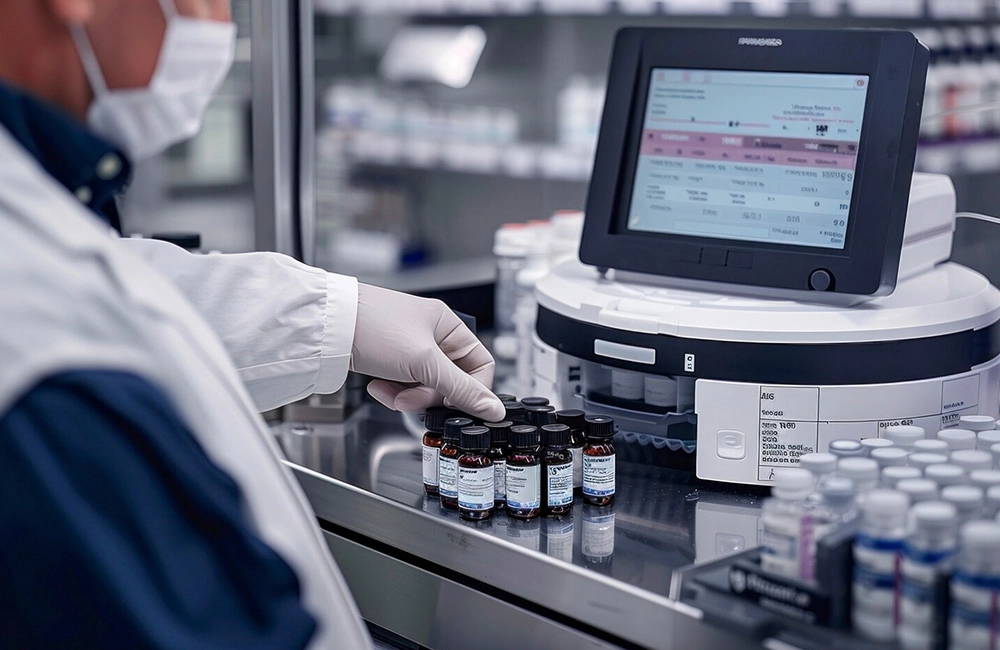
A Complete Guide to Liquid Soap Production Line, Liquid Soap Equipment Manufacturers, Solutions, and Homogenizer Mixing Tank
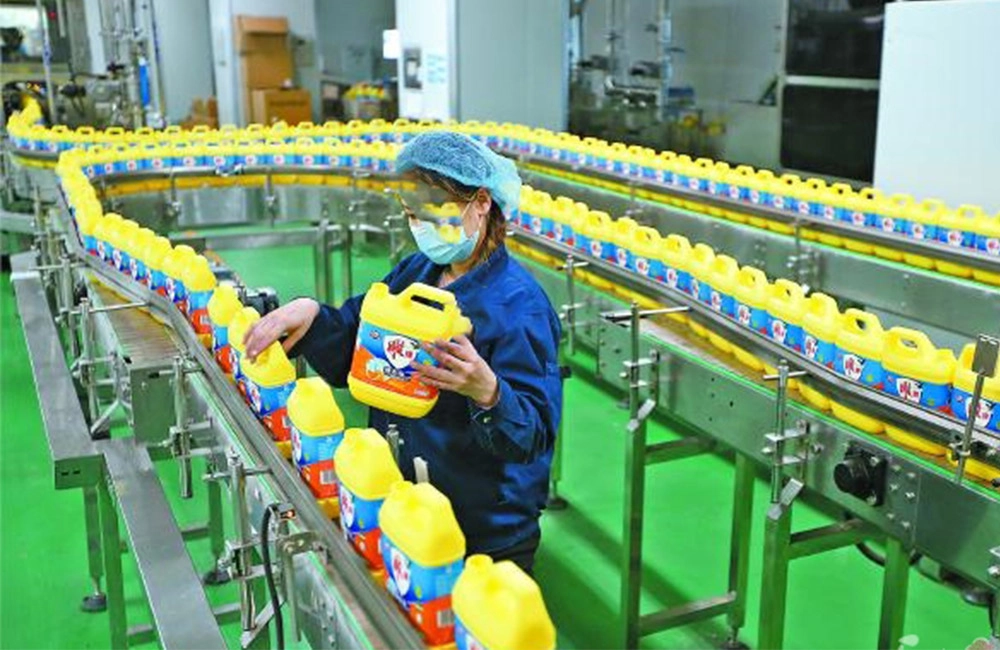
A Complete Guide to the Liquid Soap Production Line: Equipment, Process, and Key Considerations
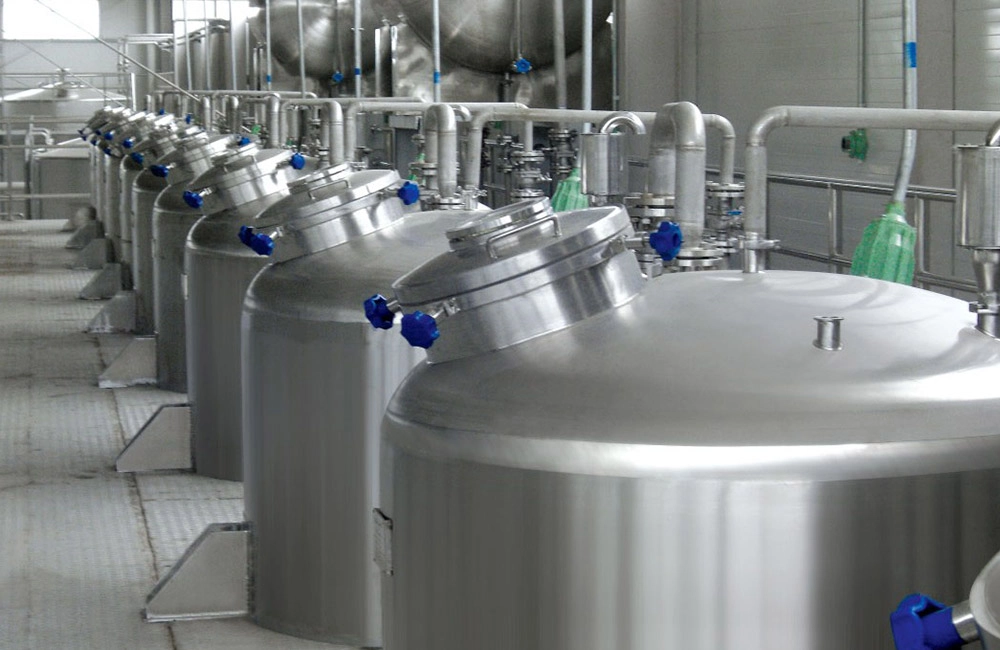
The Ultimate Guide to Liquid Mixing Tanks: Structure, Features, and Applications
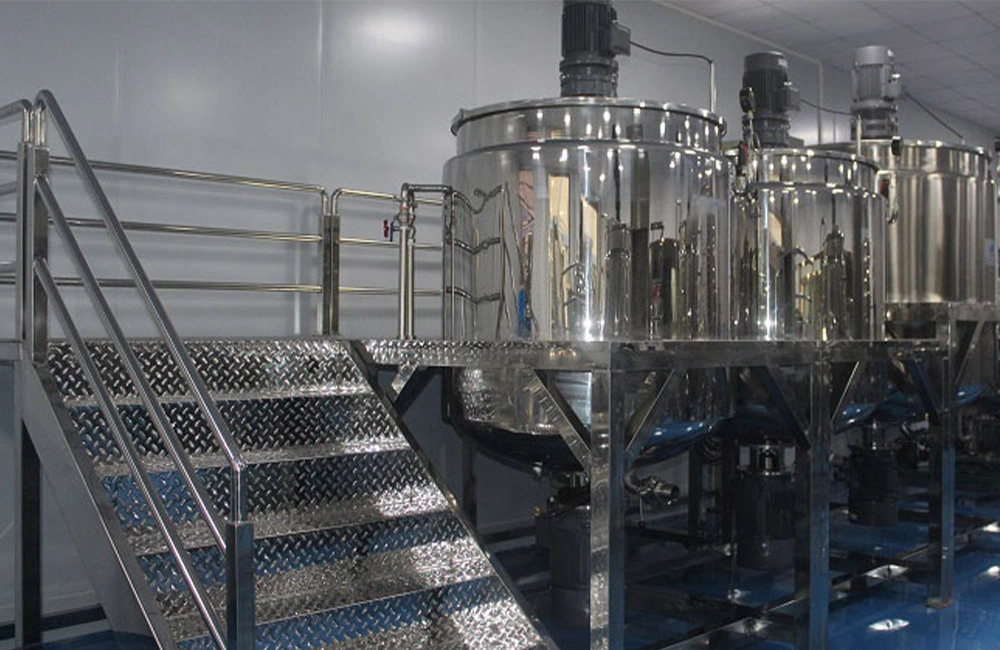
Everything You Need to Know About Homogenizer Mixer Machines: Benefits, Applications, and More
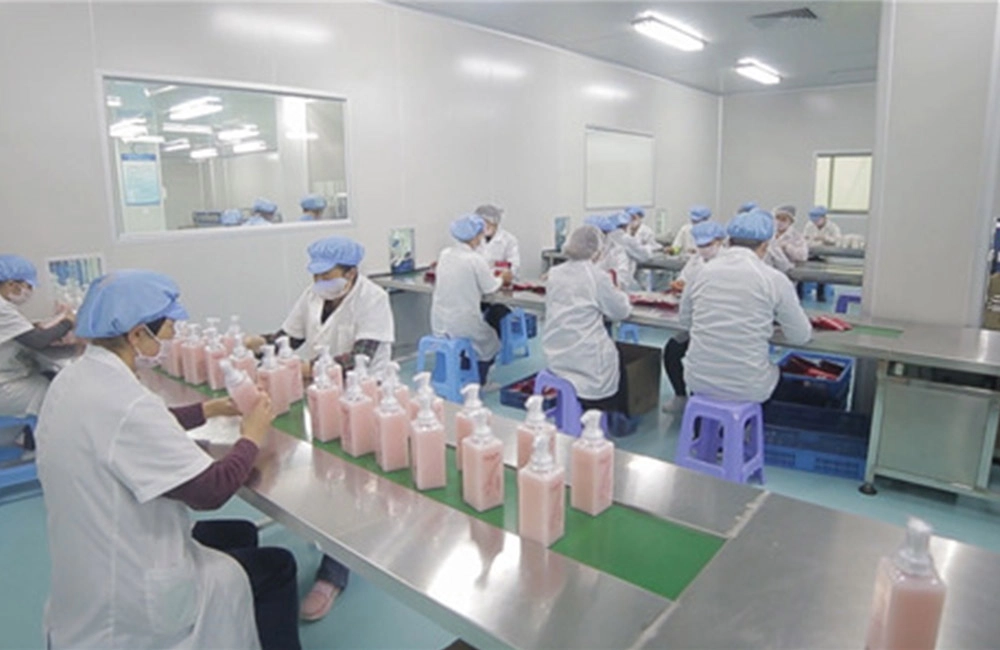
The Ultimate Guide to Cosmetic Production Line: Efficiency, Innovation, and Quality
Cosmetic
Can your equipment integrate with existing production lines?
Yes. Our equipment can seamlessly integrate with your existing production lines, ensuring smooth operation without disruptions.
Vacuum Homogneizer
Can you explain the difference between homogenizer mixing tank and agitator mixing tank?
Homogenizer mixer is also called high shear mixer, whose core function is micronization and homogenization. The homogenization process enables the dispersion size in the suspension or emulsion to be micron fine particles by mechanical force of rotor and stator, thereby improving the stability and uniformity of the product.
The agitator mixing tank is just with normal blending function, just mix different materials together, but can’t mix two incompatible liquids together.
Homogenizer Mixing Tank with Circulation System
I don’t need homogenizer, can you reduce it?
Yes, the homogenizer is an optional function, whether clients need it depends on your own products.
FAQs
What’s your advantages
We have over than 15 years of manufacturing experience for complete set of production line machines with professional team and technical staffs. Our professional solutions,details-focused services,customization capability,strict quality control process, fast and patient response,which wins the trust of various overseas customers. Yuany Machinery is always one of your first choice for win-win cooperation.
High shear homogneizer
Can the working head parts be dismountable?
Yes, the homogenizer head is dismountable. If there is any problem of the working head, just disassemble it and check. Videos is provided.
Leave a message
Have any questions or concerns about our products? Please leave us a message here, and our team will get back to you promptly.
Facebook
YouTube
LinkedIn
Whatsapp: +8613434139712