A Complete Guide to Liquid Soap Production Line, Liquid Soap Equipment Manufacturers, Solutions, and Homogenizer Mixing Tank
Discover the essentials of a liquid soap production line, from Liquid soap production line machines to liquid soap equipment manufacturer to liquid soap mixer (homogenizer mixing tank), with expert one-stop solution efficient production.
- The Growing Demand for Liquid Soap Production Lines
- What is a Liquid Soap Production Line?
- Key Stages in Liquid Soap Production
- Role of a Liquid Soap Equipment Manufacturer
- Why Partner with a Solutions Provider?
- Why Is a Homogenizer Mixing Tank Crucial in Liquid Soap Production?
- How Does a Homogenizer Mixing Tank Work?
- Choosing the Right Homogenizer Mixing Tank for Your Production Line
- 1. Size and Capacity
- 2. Material Compatibility
- 3. Energy Efficiency
- The Benefits of Automating the Liquid Soap Production Line
- Key Benefits of Automation
- Liquid Soap Production Line: Essential Equipment
- 1. Mixing Vessels
- 2. Heat Exchangers
- 3. Filling and Packaging Machines
- Key Considerations When Setting Up a Liquid Soap Production Line
- 1. Regulatory Compliance
- 2. Raw Material Sourcing
- 3. Maintenance and Support
- 4. Storage Tanks
- Conclusion: Efficient Liquid Soap Production with the Right Equipment and Solutions
- FAQs
The Growing Demand for Liquid Soap Production Lines
The liquid soap industry has grown tremendously in recent years, driven by increasing hygiene awareness and changing consumer preferences. For businesses looking to meet the demand for high-quality liquid soap, an efficient liquid soap production line is essential. Whether you are a small-scale producer or a large manufacturer, understanding the components of the production line, such as liquid soap mixer (homogenizer mixing tank) and the role of an experienced solutions provider, is crucial for optimizing production.
In this guide, we will explore the key elements of liquid soap production, focusing on the role of the manufacturer, the benefits of a liquid soap mixer (homogenizer mixing tank), and how to choose the best solutions for your business needs.
What is a Liquid Soap Production Line?
A liquid soap production line refers to the entire process, from the formulation of soap ingredients to the packaging of the final product. This includes several stages, such as water treatment, mixing, heating, homogenization, cooling, and bottling, capping, labeling, date printing and so on. Each requires specialized equipment to ensure the final soap product meets quality standards.
Key Stages in Liquid Soap Production
1. Formulation – The first step involves selecting and mixing raw materials such as oils, fats, surfactants, and water. The formulation must be precise to achieve the desired consistency and cleansing properties of the soap.
2. Mixing & Homogenization – After the formulation, the ingredients are mixed thoroughly to ensure uniformity. This is where a homogenizer mixing tank plays a vital role in achieving smooth texture and consistency.
3. Saponification & Heating – The soap mixture undergoes saponification, a chemical reaction that turns fats into soap. Heat is applied to speed up this process.
4. Cooling & Filtration – Once the soap is produced, it is cooled and filtered to remove any impurities.
5. Packaging – Finally, the liquid soap is transferred to storage tank, then to be filled into bottles or container or bags and get bottle sealed and cap closed tightened, then labeled for sale.
Role of a Liquid Soap Equipment Manufacturer
Choosing a reliable liquid soap equipment manufacturer is one of the most important decisions when setting up a production line. An experienced manufacturer can help streamline the entire production process, offering everything from equipment to turnkey solutions.
Why Partner with a Solutions Provider?
A manufacturer that also acts as a solutions provider offers comprehensive services, from equipment design to installation and after-sales support. By working with a solutions provider, you ensure that your production line is optimized for efficiency, quality, and scalability. The key benefits of working with a solutions provider include
Custom Solutions: Tailored designs for specific production needs.
End-to-End Support: Assistance with installation, training, and troubleshooting.
Cost Efficiency: Minimized downtime and waste due to optimized processes.
High-Quality Equipment: Access to the latest technology and machinery.
Why Is a Homogenizer Mixing Tank Crucial in Liquid Soap Production?
The homogenizer mixing tank is one of the most important components in a liquid soap production line. It ensures that the soap mixture is evenly blended, resulting in a smooth and stable final product. Without proper homogenization, the soap might separate or have an inconsistent texture, leading to a poor consumer experience.
How Does a Homogenizer Mixing Tank Work?
A homogenizer mixing tank uses high-pressure shear force to break down the particles in the soap mixture, creating a uniform consistency. The tank is equipped with a rotor-stator system that helps in emulsifying and dispersing ingredients evenly. This is especially important for liquid soap production, where the soap’s texture and stability are critical for consumer appeal.
Choosing the Right Homogenizer Mixing Tank for Your Production Line
When selecting a homogenizer mixing tank, it’s essential to consider the scale of your production, the types of ingredients you use, and the desired output. Here are some factors to keep in mind when choosing the right tank:
1. Size and Capacity
Depending on the volume of soap you plan to produce, the size and capacity of the homogenizer mixing tank must be aligned with your production goals. Larger tanks are suitable for high-volume production, while smaller tanks are ideal for boutique or specialty soap brands.
2. Material Compatibility
Ensure that the tank material is compatible with the raw ingredients you use. For example, stainless steel tanks are commonly used in the food, chemical, cosmetic, and pharmaceutical industries due to their durability and resistance to corrosion.
3. Energy Efficiency
Modern homogenizer mixing tanks are designed to be energy-efficient, reducing operating costs and minimizing environmental impact. Look for energy-saving features such as advanced motor control systems.
The Benefits of Automating the Liquid Soap Production Line
Automation has become a key factor in improving efficiency and reducing costs in liquid soap production. An automated production line can help businesses scale up production while maintaining consistent product quality.
Key Benefits of Automation
1. Increased Production Speed – Automated systems can operate continuously, significantly increasing production speed.
2. Consistency and Quality Control – Automation ensures that each batch of soap is produced with the same level of quality, reducing human error.
3. Reduced Labor Costs – With automation, fewer workers are required, which lowers operational costs.
4. Energy Efficiency – Automated systems can be optimized for energy use, leading to reduced utility expenses.
Liquid Soap Production Line: Essential Equipment
In addition to the homogenizer, several other essential element for a liquid soap production line. These include:
1. Mixing Vessels
Mixing vessels are used to combine raw materials before the homogenization process. They are equipped with agitators that help in mixing viscous ingredients.
2. Heat Exchangers
Heat exchangers are used to heat the soap mixture during saponification and cooling it down after the process is complete.
3. Filling and Packaging Machines
These machines are responsible for filling liquid soap into bottles and containers. They can be automated or semi-automated, depending on production volume.
Key Considerations When Setting Up a Liquid Soap Production Line
Setting up a liquid soap production line requires careful planning and consideration. Here are the most important factors to keep in mind:
1. Regulatory Compliance
Ensure that your production line complies with industry regulations and quality standards. This includes adhering to safety protocols, environmental regulations, and production certifications.
2. Raw Material Sourcing
Identify reliable suppliers for the raw materials needed for soap production, such as surfactants, oils, and fragrances.
3. Maintenance and Support
Choose equipment from a manufacturer or solutions provider who offers ongoing maintenance and technical support to ensure your production line runs smoothly over time.
4. Storage Tanks
Storage tanks are used to store the finished liquid soap before it is packaged.
Conclusion: Efficient Liquid Soap Production with the Right Equipment and Solutions
To succeed in the liquid soap industry, businesses need to invest in an efficient and high-quality production line. From selecting the right homogenizer mixing tank to partnering with a reliable manufacturer and solutions provider, every element of the production process plays a crucial role in delivering consistent, high-quality liquid soap. With the right equipment, including automated systems and homogenizer tanks, you can streamline production, reduce costs, and meet the growing demand for liquid soap products in the market.
FAQs
1. What is the role of a homogenizer mixing tank in liquid soap production?
A homogenizer mixing tank ensures that ingredients are evenly mixed, creating a smooth and stable liquid soap product.
2. How can automation improve my liquid soap production line?
Automation increases production speed, ensures consistency, reduces labor costs, and improves energy efficiency.
3. What should I look for when choosing a liquid soap manufacturer?
Look for a manufacturer who offers custom solutions, end-to-end support, high-quality equipment, and expertise in the industry.
4. What other equipment is required for a complete liquid soap production line?
In addition to the homogenizer mixing tank, other equipment includes mixing vessels, heat exchangers, filling machines, and storage tanks.
5. How do I ensure my liquid soap production line meets regulatory standards?
Ensure that your production process adheres to local and international safety and quality regulations, and work with a manufacturer who understands these requirements.
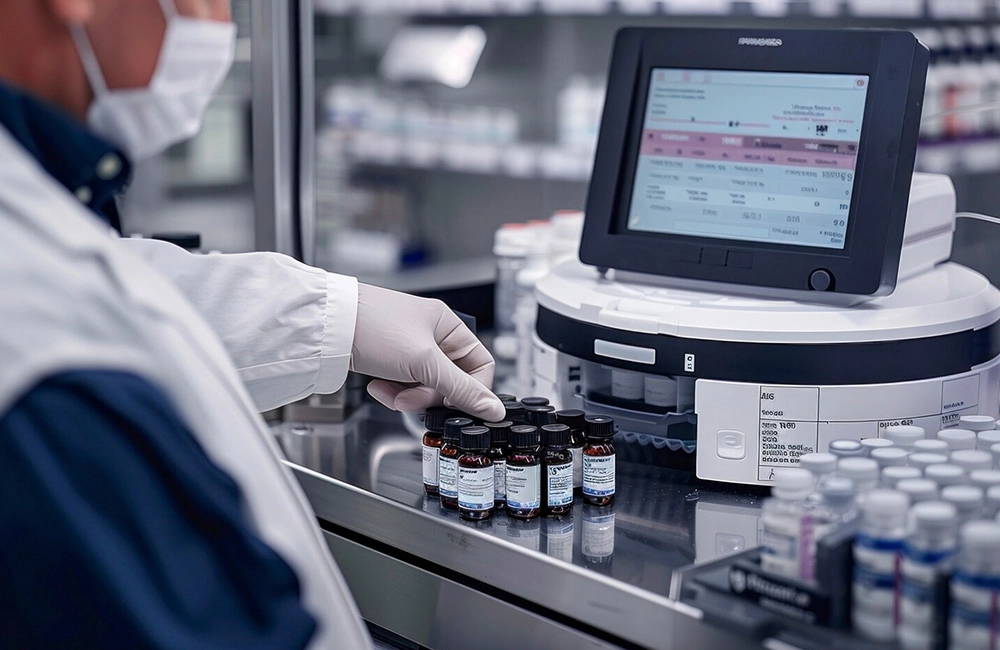
Regular Questions Asked by a Buyer and Answers About Liquid Production Line
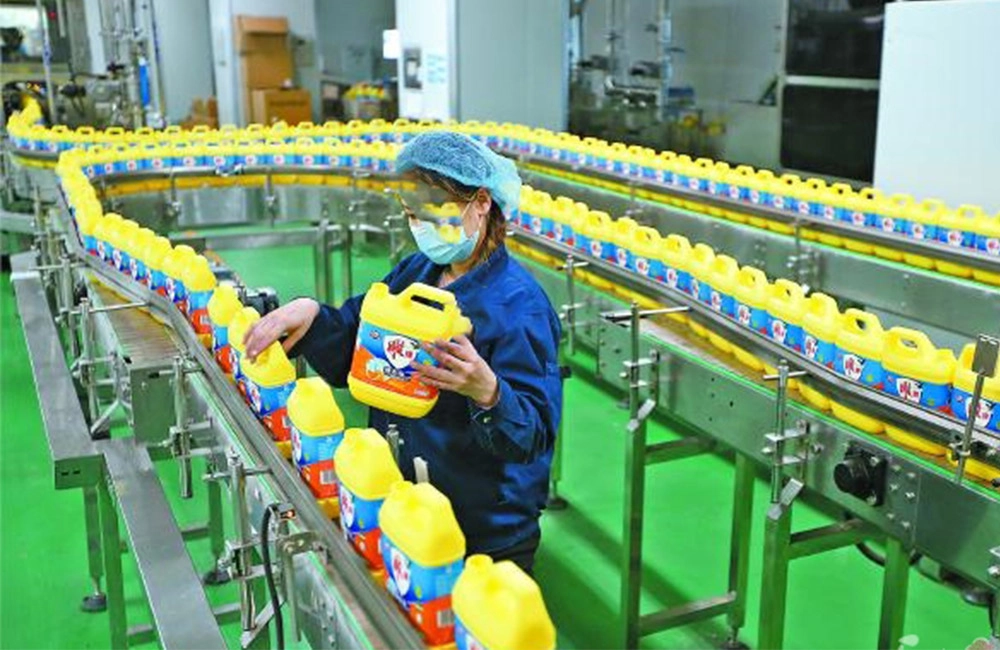
A Complete Guide to the Liquid Soap Production Line: Equipment, Process, and Key Considerations
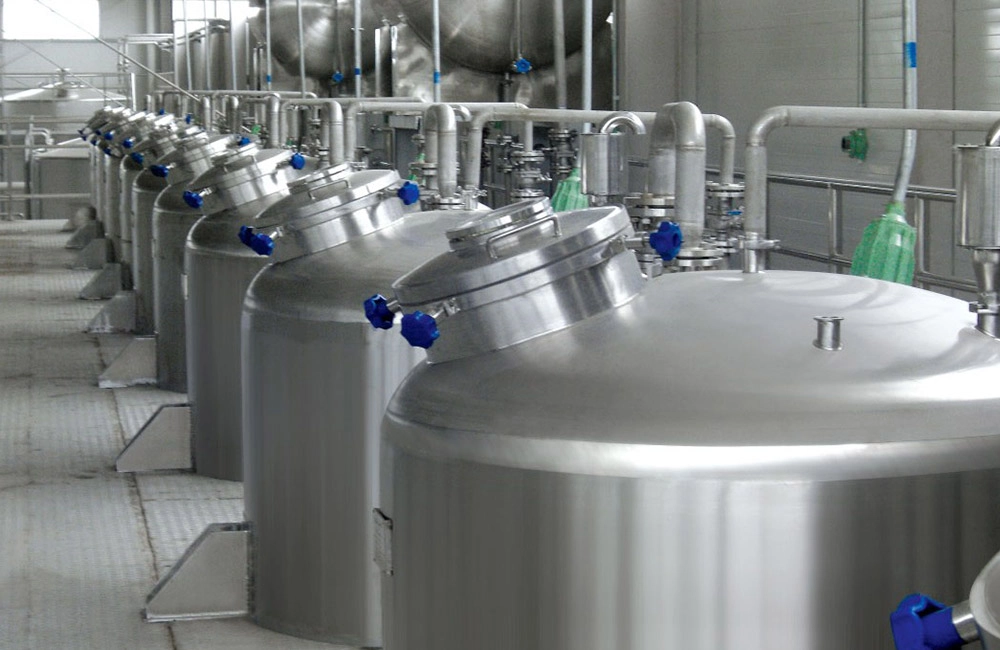
The Ultimate Guide to Liquid Mixing Tanks: Structure, Features, and Applications
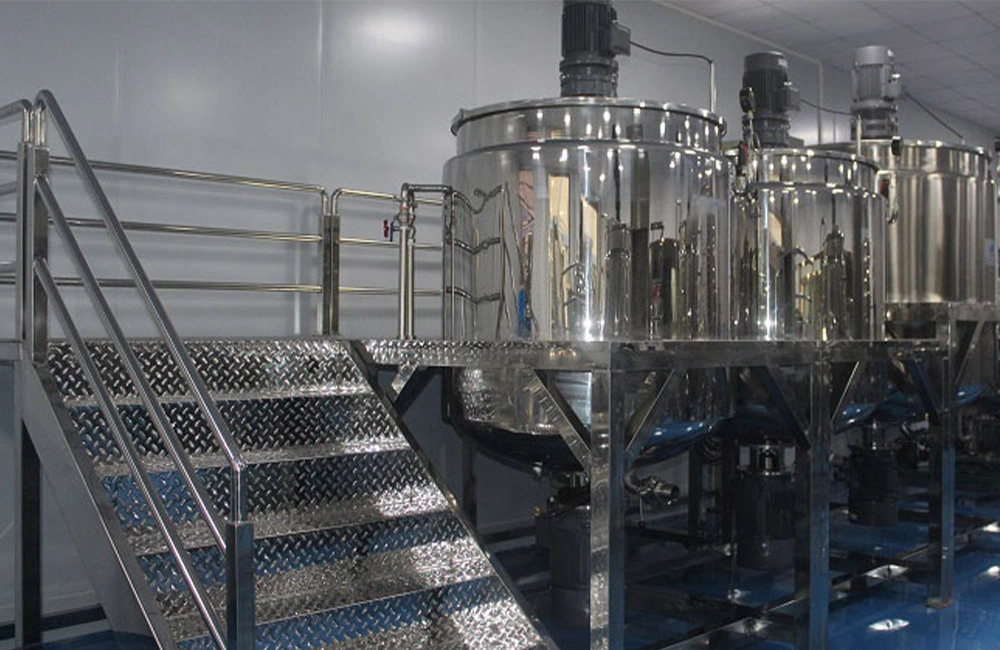
Everything You Need to Know About Homogenizer Mixer Machines: Benefits, Applications, and More
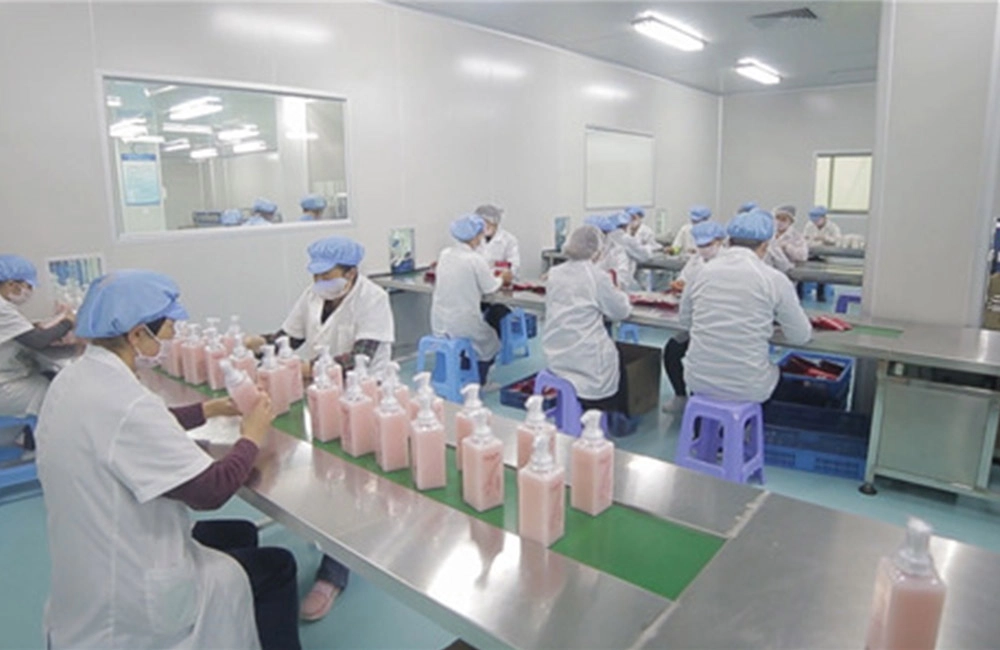
The Ultimate Guide to Cosmetic Production Line: Efficiency, Innovation, and Quality
Vacuum Emulsifier
What the difference between hydraulic lifting vacuum mixer and fixed lid vacuum mixer?
The main different between the two types of equipment is on the main emulsifier pot. The main pot of hydraulic lifting emulsifier can tilt down to empty materials. The hydraulic system helps to lift the main pot cover up, then the main pot can tilt down. But the fixed lid type has no this function.
Semi automatic powder filling machine
What’s the capacity of the material hopper of this filling powder machine?
The standard hopper capacity is 50L.
Desktop Bottle Sealing Machine
Is the height of the bottle cap sealing machine adjustable?
Yes, there is a handle wheel to adjust the height of sealing head according to different bottle height.
Liquid Mixing Tank
Is there any temperature control? Can I set a targeted temperature?
Yes,there is temperature control display and controller on the control panel. Before heating operation, just set a temperature that you want, it can keep constant temperature;
Ink Jet Printer
What package materials are required for this date printing machine?
The dater printer is suitable for various coated cardboard, film, non-coated, coated paper, aluminum foil, plastic card, self-adhesive, PP, PET, PVC, PE, etc
Leave a message
Have any questions or concerns about our products? Please leave us a message here, and our team will get back to you promptly.
Facebook
YouTube
LinkedIn
Whatsapp: +8613434139712